DLIP - Technology
Overview
In Direct Laser Interference Patterning, or short DLIP, laser beams are combined in a controlled manner to create a defined interference pattern within the machining area. The pattern produced is much smaller than the laser beam itself with typical resolutions ranging from 300 nm to 30 µm. Because of the interference effect, there are areas of high intensity (interference maxima) and zero intensity (interference minima) within the laser beam. During processing, the material surface is only modified at the intensity maxima, the remaining areas remain typically unmodified.
The patterns created with our DLIP technology can be transferred into almost any material, from metals to polymers to ceramics, coatings and glass. The realized structures are created in a one-step process and are often comparable to known structures on natural surfaces such as lotus leaf and moth eye.
Why laser technology?
In general, lasers can enable high-precision machining of surfaces so that tailored surface properties can be addressed. In contrast to photolithography, coating, etching or sandblasting processes, laser technologies offer the following advantages:
- Non-contact processing of surfaces
- Typically no chemicals or clean room conditions required
- Often more sustainable solution compared to established processes

Why our solution?
Our DLIP solutions offer further decisive advantages over established laser processes such as conventional laser microstructuring. These consist of completely new surface functions, which can be applied to technical surfaces at high speed. Further advantages are:
- Many functions addressable by bio-inspired micro- and nanostructures
- Large-scale functionalization of 2D and 3D components
- High speed machining with speeds up to 3 m²/min
- Our DLIP technology has already been installed many times around the world in compact system solutions
Structures
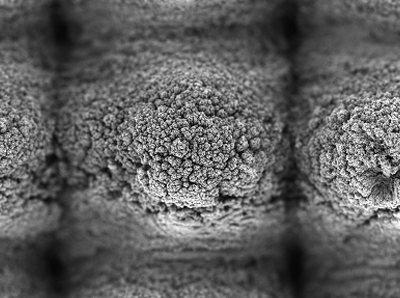
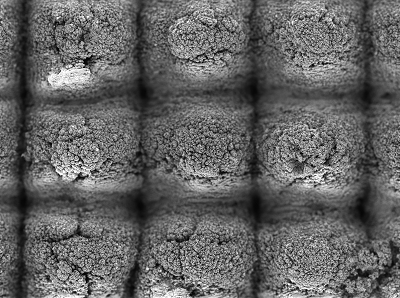
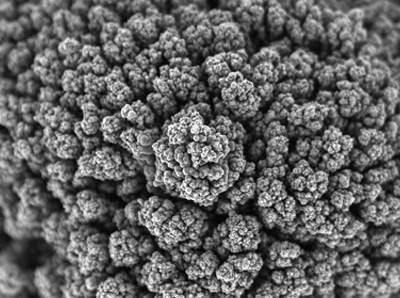
Almost any material can be treated with our DLIP technology solutions including metals, polymers, ceramics, composites, coatings and glass. The available surface geometries range from single-scale structures such as line-like, point-like, and cross-like configurations to more complex hierarchical surface structures combining different length scales.
Each of the surface structures has a unique impact on surface performance, which consequently leads to surface improvements such as anti-icing, improved biocompatibility or a defined surface decoration.
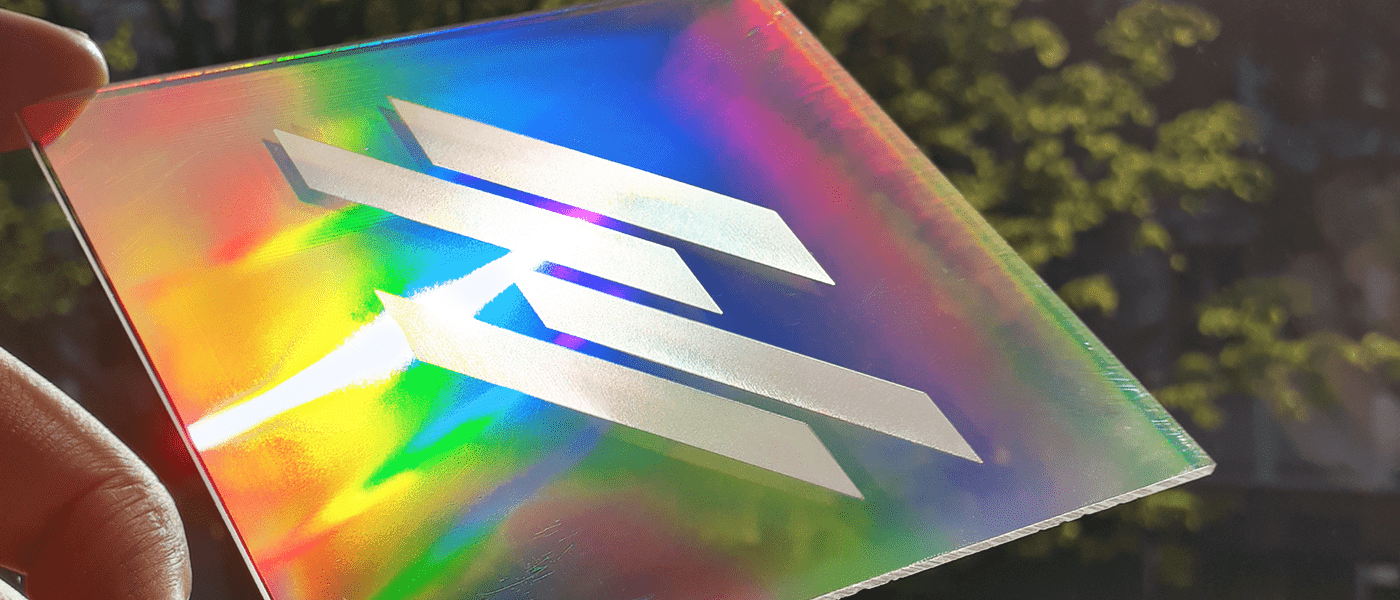
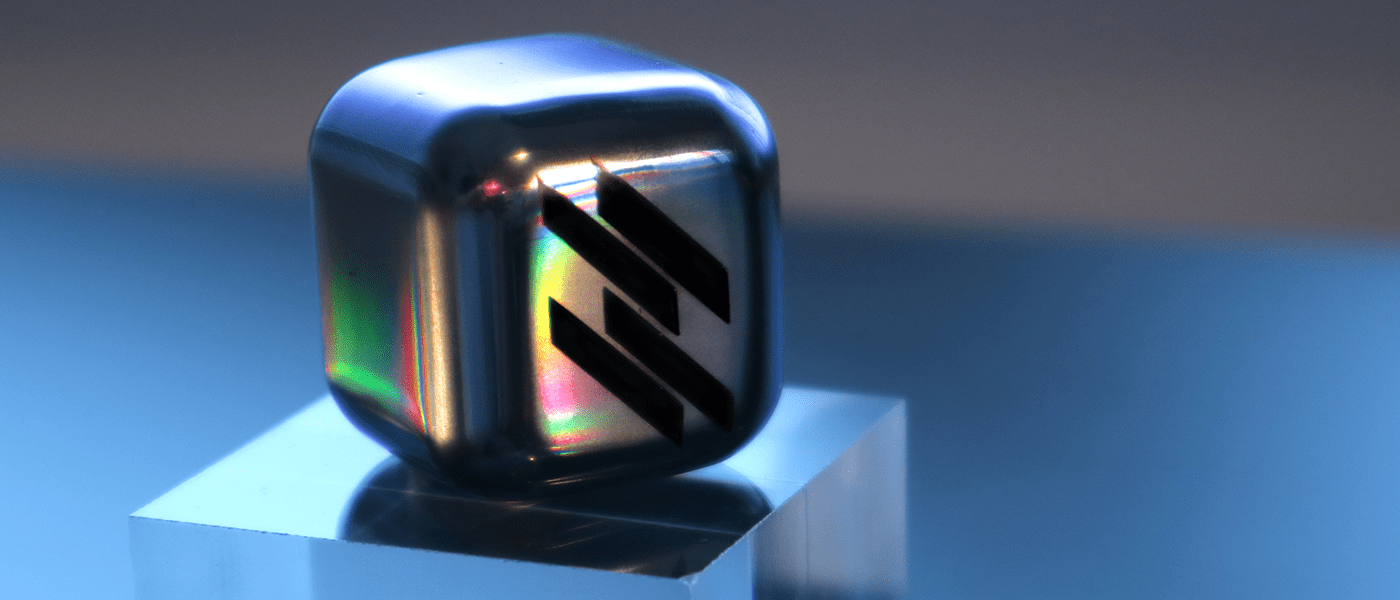
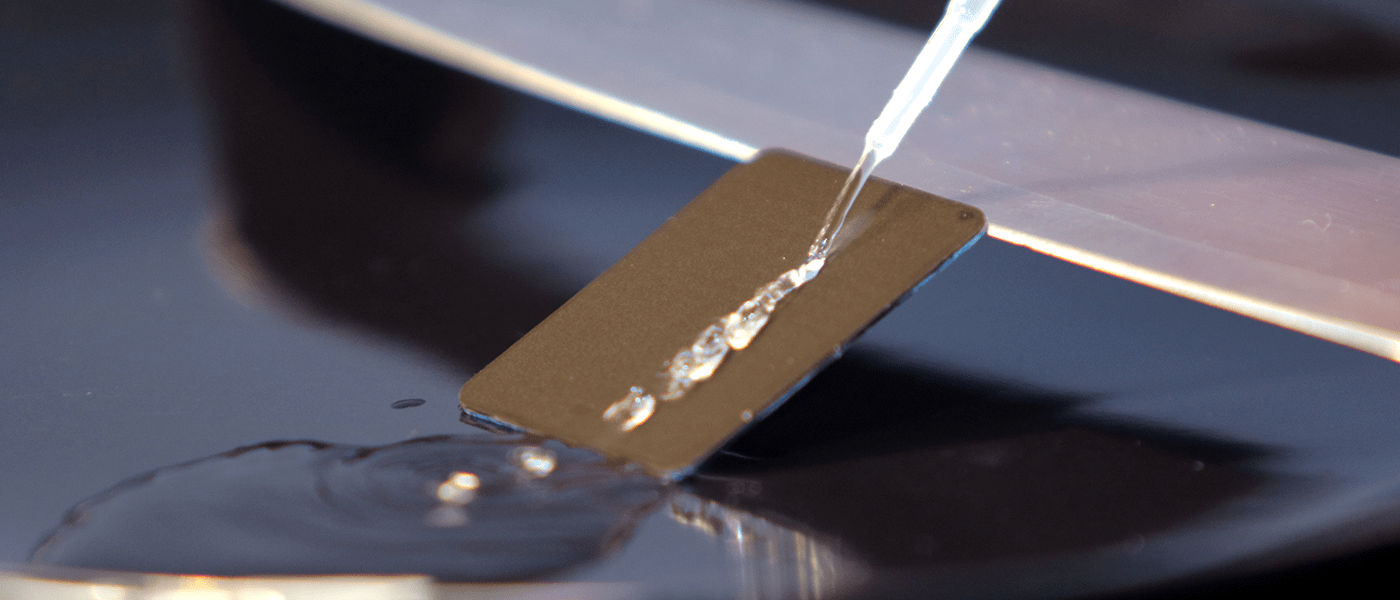
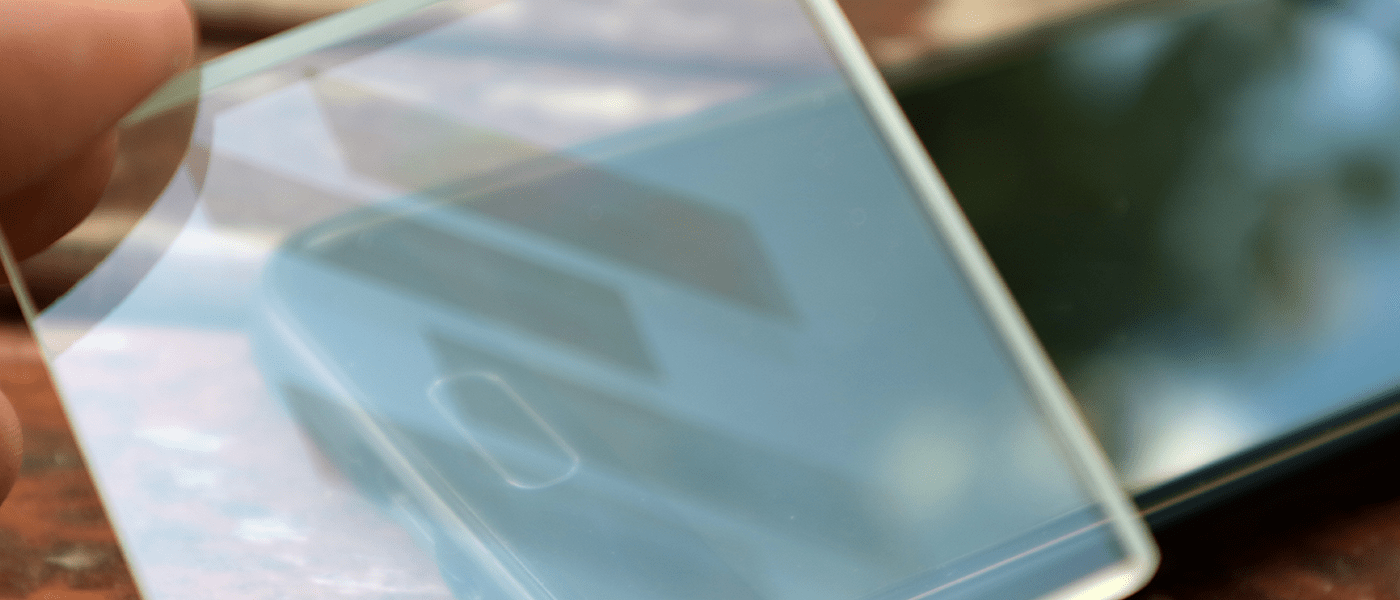
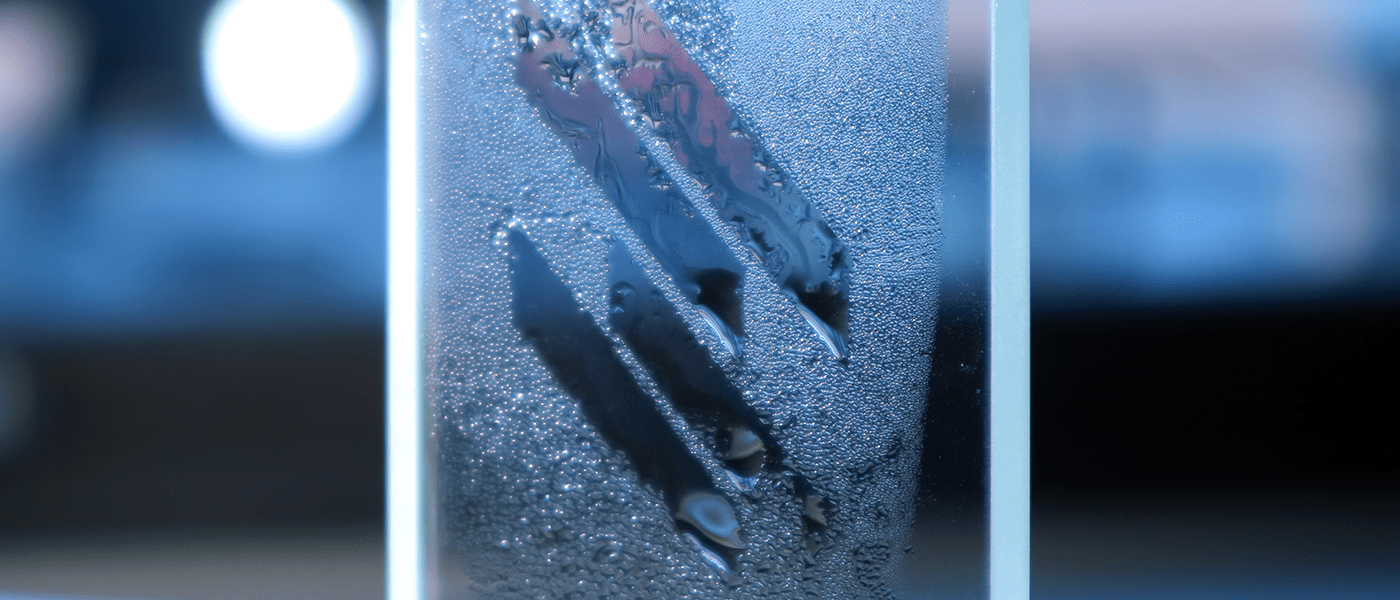
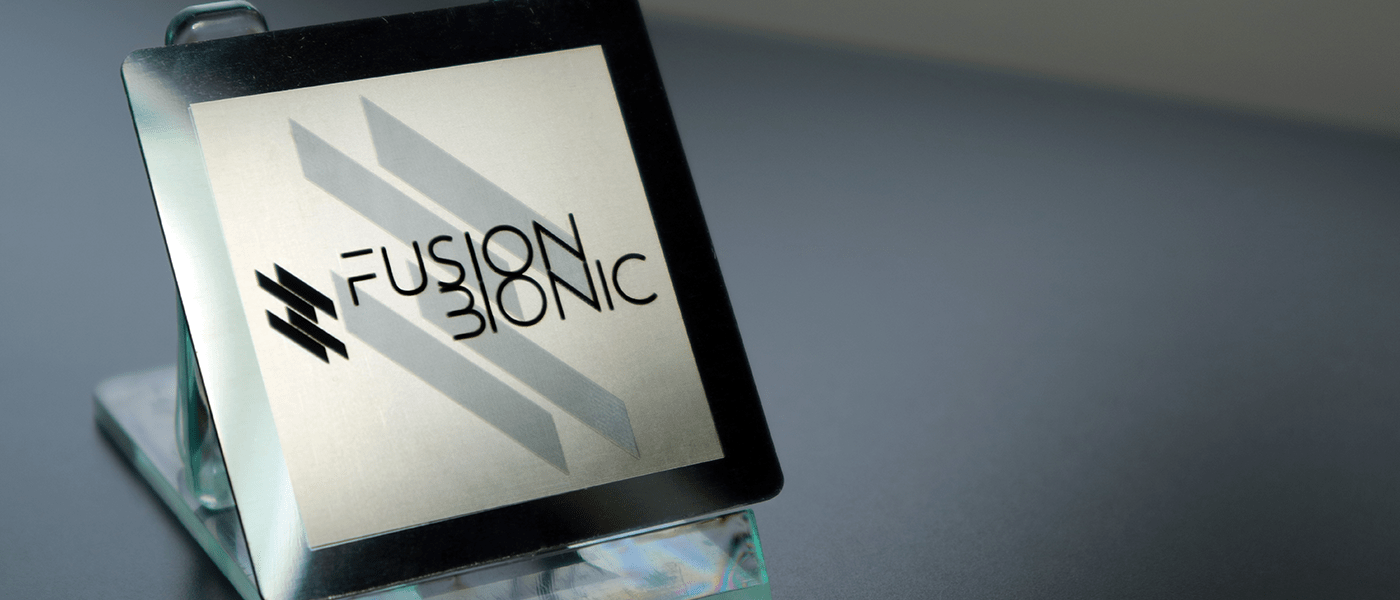
Most conventional laser sources such as short and ultra-short pulse lasers are compatible with DLIP technology, making the texturing process burr-free and reducing heat generation. We offer various DLIP hardware solutions through our patented compact modules, which can be integrated into existing machines without internal optical adjustments. Our product series is compatible with most CNC machines and can also be combined with industrial robotic arms and roll-to-roll solutions.