Automotive industry
Innovation drivers
The automotive sector is often an innovation driver with a high impact on other industry sectors. The components and parts used must be extremely reliable, which requires continuous improvement of the manufacturing processes used. For example, increasing electrification in automotive engineering increases the demands on the functionality of electrical subsystems. This is often only given if the plug connections used are reliable even under extreme conditions such as vibrations and environmental influences. In other areas, such as environmental detection using LIDAR and radar systems, it must be ensured that the systems will function even under extreme weather conditions.
Advantages
Advanced surface engineering can make the decisive difference in the achievable performance. By applying micro- and nanostructures using DLIP technology, it could be shown that the electrical contact resistance of electrical plug contacts could be significantly reduced in certain contact scenarios. This significantly improves the reliability of plug contact systems. In the area of environmental detection, targeted surface structuring can lead to improved visual performance, since disturbing environmental effects such as condensation or dirt deposits can be reduced.
- Resistance reduction by up to 80%
- Reduction of dirt build-up and condensation
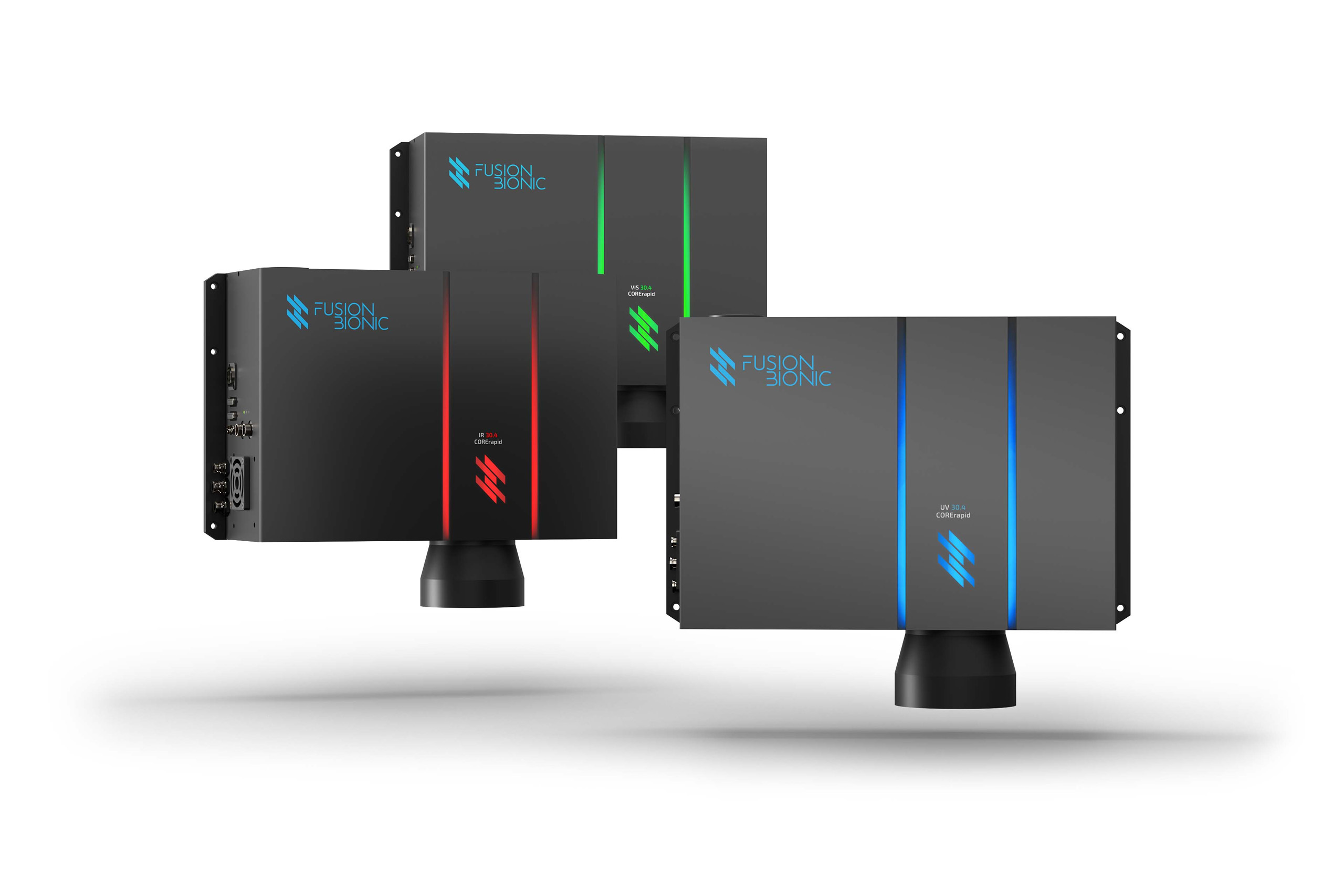
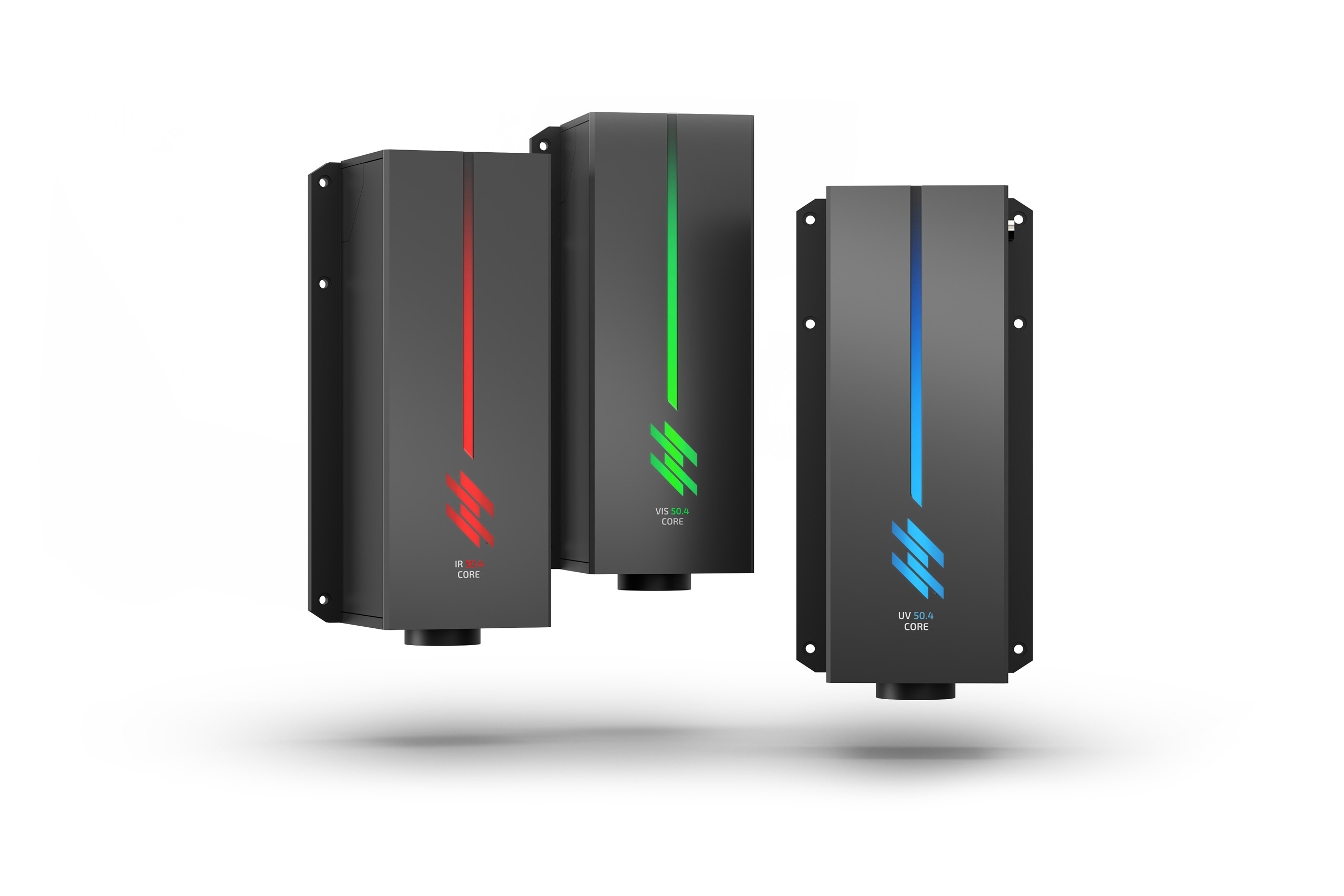
Why our solution?
The application of functional laser structures to automotive components and subsystems can contribute to a performance gain.
- Non-contact processing
- Precise energy input
- Flexibility in surface design
- Low environmental impact
While several laser approaches are already available on an industrial scale, with DLIP we offer a completely different solution as a new standard for surface functionalization.